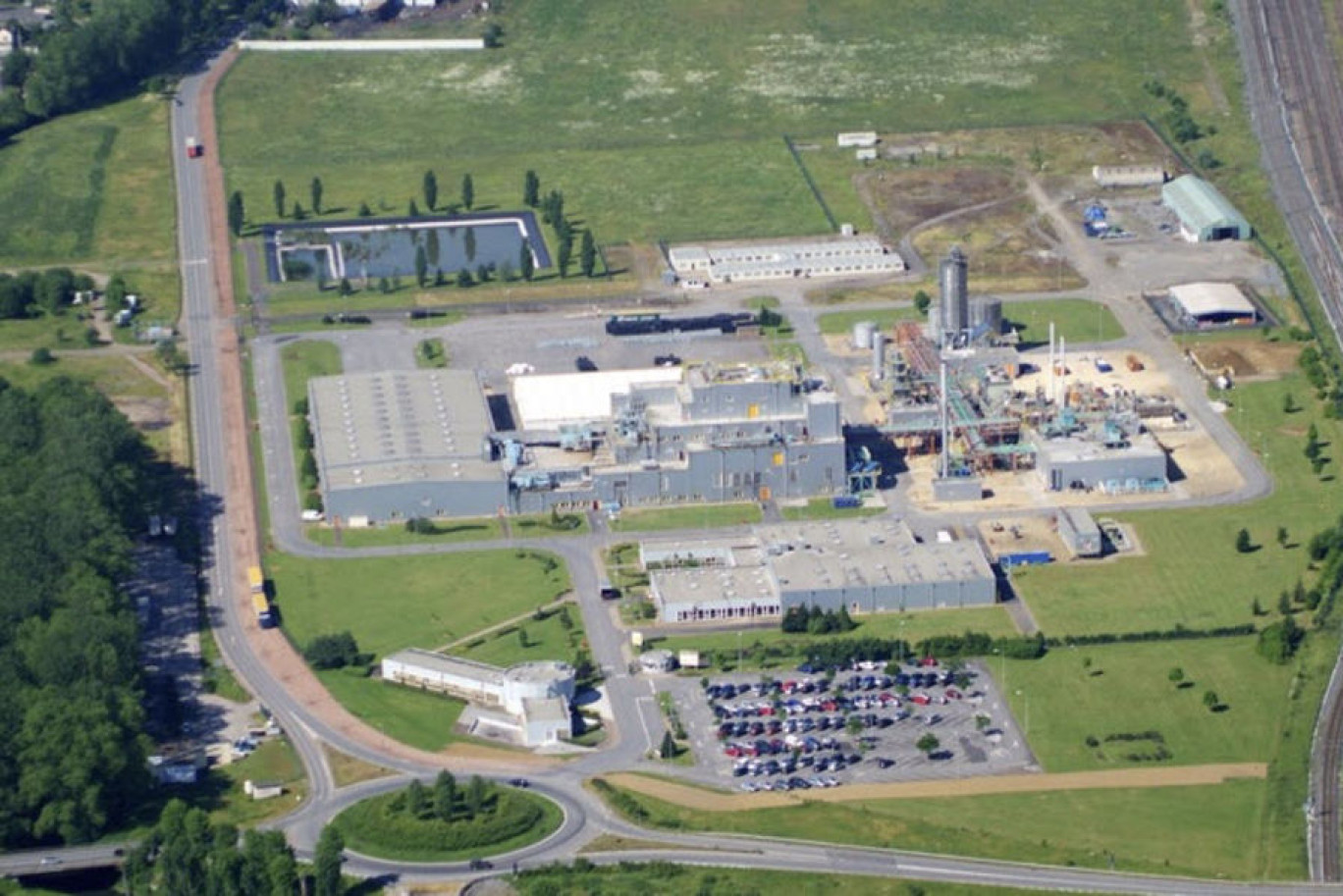
Information
- Client: Indorama
- Date: Jun 2022
- Duration: 6 Months
- Category: Industrial
The Project
Indorama Ventures in Longlaville is a leading manufacturer of durable technical textiles for industrial, tire reinforcements, and specialty applications globally.
The implementation of iConnect4.0 played a pivotal role in establishing seamless communication between the Programmable Logic Controller (PLC) systems employed within the plant. By acting as a dynamic bridge between various PLCs, iConnect4.0 facilitated the exchange of critical real-time data, fostering enhanced synchronization and coordination among different stages of the production line. This cohesive integration streamlined plant operations, enabling swift decision-making and minimizing disruptions for improved efficiency.
Moreover, iConnect4.0's prowess extended beyond the factory floor. The software's ability to collate and process data efficiently was leveraged to provide crucial insights to the plant's logic systems. By facilitating the flow of accurate and timely information, iConnect4.0 empowered the plant's logic to make informed decisions, optimize processes, and maintain stringent quality standards. Furthermore, this symbiotic communication extended to the business aspect, as iConnect4.0 seamlessly transmitted pertinent data to the business operations. This two-way flow of information bridged the gap between shop floor realities and strategic decision-making, fostering a more holistic and informed approach to operational management.
In the context of Indorama Ventures in Longlaville, iConnect4.0 stands as a technological cornerstone that not only unites PLC systems for streamlined operations but also drives intelligent data sharing that elevates both plant logic and business strategies to new heights of precision and effectiveness.
The Challange Was
However, behind the scenes, a significant challenge presented itself. Integrating iConnect4.0 with the diverse Programmable Logic Controller (PLC) systems used within the plant was not without its complexities. The PLCs had different communication protocols, data formats, and operational standards, which posed a significant hurdle in establishing a seamless connection. Bridging these disparate systems required a thoughtful approach to ensure that the data exchange was accurate, synchronized, and compatible with the various PLC configurations present in the manufacturing environment. This challenge called for innovative solutions to harmonize these diverse elements and enable iConnect4.0 to communicate effectively with each PLC, ensuring that the plant's operations were truly interconnected and optimized.
Our solutions Was
To tackle this intricate challenge head-on, our team devised a comprehensive solution that harmonized the varied PLC systems with iConnect4.0, transforming the obstacle into an opportunity for enhanced connectivity and operational efficiency.
Our solution centered around the development of a versatile middleware layer that acted as a translation hub. This middleware layer effectively translated the different communication protocols, data formats, and standards used by the various PLCs into a unified language that iConnect4.0 could comprehend. By implementing protocol converters, data normalization techniques, and dynamic mapping algorithms, we created a bridge that allowed iConnect4.0 to seamlessly communicate with each PLC, irrespective of its individual specifications.
Furthermore, the middleware layer employed advanced data buffering mechanisms to ensure that data flows remained consistent and synchronized, minimizing delays and discrepancies in real-time information exchange. This synchronization was particularly crucial for maintaining accurate plant logic and informed decision-making.
Our solution not only established a harmonious connection between iConnect4.0 and the diverse PLCs but also enabled bidirectional data flow. It allowed iConnect4.0 to gather critical operational data from the PLCs and transmit relevant insights back to them, creating a closed-loop system that fostered continuous improvement and optimization.
In essence, our innovative middleware solution overcame the challenge of disparate PLC systems by serving as a unifying bridge. This approach ensured that the benefits of iConnect4.0's connectivity and data analytics were extended to all corners of the plant's operations, fostering a cohesive and synchronized manufacturing ecosystem.